Bouten en glijlagers voor bouwmachines testen: Hardox en iglide
Andrej Roskic | 30 mei 2024
Het merk Hardox®-slijtplaten wordt vaak aangetroffen in bedrijfsvoertuigen en bouwmachines waar stalen oppervlakken de zwaarste belastingen moeten doorstaan. Van het laadgebied van kiepwagens tot de laadbak van wielladers, Hardox® slijtplaten beschermen op betrouwbare wijze tegen slijtage. Daarom zijn assen en bouten gemaakt van Hardox® voor de hand liggende tegenhangers voor iglide® glijlagers, die kunnen pronken met hun onderhoudsvrije, droog werkende eigenschappen en hoge mechanische sterkte in bouwmachines en bedrijfsvoertuigen.
Aangezien verschillende paren glijlagers en bouten sterk kunnen verschillen wat betreft de slijtvastheid van de betrokken oppervlakken, hebben we bouten gemaakt van Hardox® en bussen gemaakt van iglide® onderworpen aan praktijktests.
De zware test van glijlagers
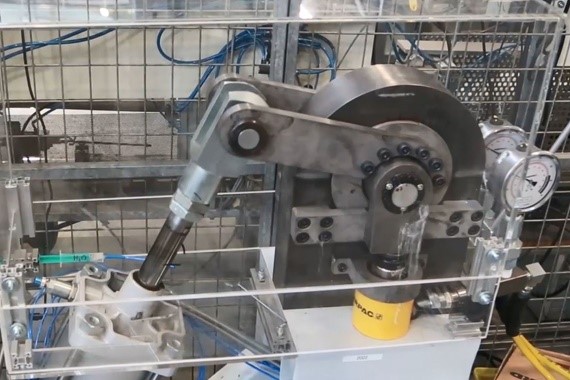
Om de levensduur van verschillende lagers te vergelijken, hebben we een reeks tests uitgevoerd. We hebben bronzen lagers met initiële smering getest op lagerbouten van Hardox® 400, naast glijlagers van iglide® Q2. Deze tests werden uitgevoerd op de igus heavy-duty testbank.
Voor de tests hebben we de bussen in een testopstelling geperst. Vervolgens hebben we ze onderworpen aan een belasting van 76MPa. Deze belasting is toegepast op de testbout, die zowel draaide als “tuimelde”. De draaihoek tijdens deze tests was 50° en we hebben het tuimelen uitgevoerd met een snelheid van 0,01 m/s.
Door deze grondige tests konden we een nauwkeurige vergelijking maken van de prestaties en levensduur van de verschillende lagers onder dezelfde omstandigheden. Dit helpt ons om beter geïnformeerde beslissingen te nemen over welke lagers het beste zijn voor specifieke toepassingen.
Het doel was om een cyclusaantal van 45.000 te bereiken om vervolgens het resulterende wanddikteverlies als slijtage te meten. Uiteindelijk kan uit dit wanddikteverlies de slijtage per afgelegde kilometer worden berekend.
Het resultaat
De test met de massief bronzen bus beëindigde voortijdig na 10.000 cycli vanwege de hoge slijtage, terwijl de iglide Q2-bus de volle 45.000 cycli doorliep. Na deze 45.000 cycli maten we een wanddikteverlies van 120 µm op de bus voor de Hardox® 400- en iglide Q2-bussen.
Dit komt overeen met een slijtage van 73 µm. De bronzen bus daarentegen vertoonde al na 10.000 cycli een wanddikteverlies van 207 µm na voortijdig afbreken. Dit komt overeen met een slijtagesnelheid van 559 µm/km.
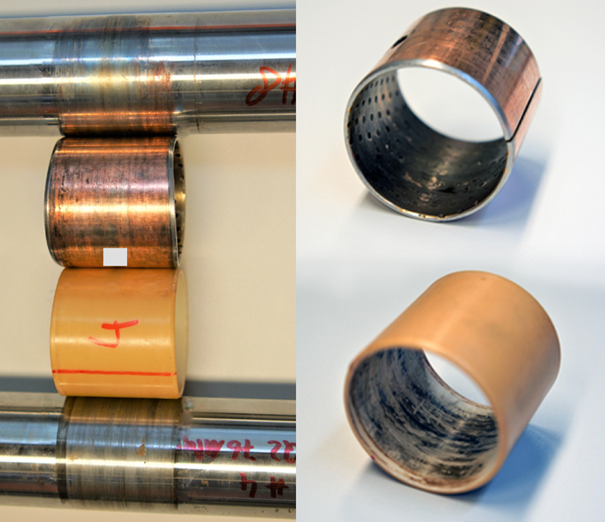
Conclusie
De combinatie van Hardox® 400 bouten met iglide Q2 bussen bleek zeer voordelig en slijtvast in de uitgevoerde test. De vereiste levensduur van 45.000 cycli werd voltooid met een goed resultaat en zonder noemenswaardige schade aan de loopvlakken.
Hebt u vragen over het gebruik van kabelrupsen in uw eigen toepassing? Neem contact op met een kabelrups expert of bel ons rechtstreeks op +31(0)346 353 932.
Voor meer informatie over kabelrupsen en lagers kunt u onze whitepapers bekijken op: